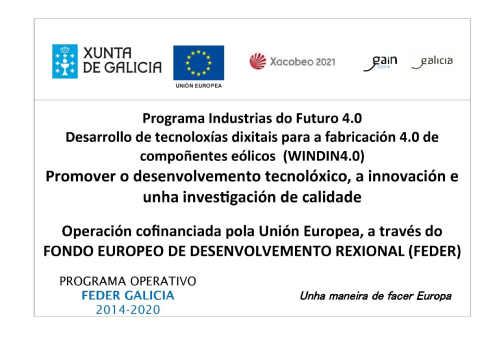
31 marzo 2022
Desarrollo de tecnologías digitales para la fabricación 4.0 de componentes eólicos (WINDIND 4.0)
El proyecto WINDIND 4.0 formado por el consorcio de GRI Towers Galicia, S.L. y Ágata Technology, S.L., tiene como objetivo el desarrollo de soluciones y subsistemas orientados al paradigma de fábrica inteligente que conformen una nueva ruta de fabricación integral de producto discreto, de gran volumen, peso y grandes dimensiones.
Se persigue alcanzar un entorno industrial digitalizado modular, flexible y adaptable que garantice la calidad, la seguridad y la trazabilidad en toda la cadena de valor de fabricación y que permita la evolución continua de los procesos de fabricación. Permitiendo agilizar la toma de decisiones basadas en datos y flexibilizar el entorno de fabricación, en todas sus etapas, a través de la consolidación de toda la información recogida.
Este proyecto cuenta con el apoyo financiero de la Unión Europea, cofinanciado con cargo a los Fondos de Desarrollo Europeo Regional (Feder) en el marco del Programa Operativo Feder Galicia 2014-2020, subvencionado por la Agencia Gallega de Innovación y con el apoyo de la Vicepresidencia Segunda e Conselleria de Economía, Empresa e Innovación.
ANUALIDAD 2021
Durante el primer hito del proyecto WINDIN4.0 del programa “Fábrica do futuro, fábrica intelixente e sostible da industria 4.0 (cuarta convocatoria)”de GAIN, se han realizado trabajos de desarrollo que se alinean y responden a los objetivos del planteados en el proyecto en cuanto a tres ejes principales:
•Desarrollo de soluciones y subsistemas orientados al paradigma de fábrica inteligente que conformen una nueva ruta de fabricación integral de producto discreto, de gran volumen, peso y grandes dimensiones en escenarios industriales VUCA como el sector eólico. En el primer paquete de trabajo del proyecto se han estudiado el proceso integral de gestión de proyecto de fabricación de torres eólicas desde diferentes puntos de vista como la fabricación, gestión del proyecto, digitalización de proceso manuales que confluyen en la generación de conocimiento en cuanto a las posibilidades tecnológicas existentes y su aplicabilidad el sector industrial especifico que se plantea
•Desarrollo de un entorno industrial digitalizado modular, flexible y adaptable que garantice la calidad, la seguridad y la trazabilidad en toda la cadena de valor de fabricación y que permita la evolución continua de los procesos de fabricación. En este sentido en los paquetes de trabajo 2,3 y 4 se han definido por completo y comenzado el desarrollo de algunas soluciones digitales orientadas a la gestión características estructurales del producto,, gestión de procesos fabricación,, digitalización de defectologia y mediambiente y gestión integral de proyectos sobre plataforma de Ágata.
•Agilizar la toma de decisiones basadas en datos y flexibilizar el entorno de fabricación, en todas sus etapas, a través de la consolidación de toda la información recogida en el centro industrial. Los trabajos realizados durante el primer hito en cuanto a la definición y desarrollos de diferentes soluciones dotarán de las herramientas necesarias para su posterior análisis y a facilitar la toma de decisiones, sin embargo es necesario desarrollar a integrar completamente las diferentes arquitecturas para desarrollar los cuadros de mando generales que se producirá en siguientes hitos.
Debemos subrayar algunos de los retos de gestión a los que se ha enfrentado GRI y Ágata en la ejecución del proyecto. El inicio del proyecto se han enfrentado a retos organizativos relevantes provocados principalmente por el estado de pandemia mundial existente durante este año. A lo largo del año 2021, hemos continuado con las restricciones de movilidad, aforo, asistencia al centro de trabajo, etc… iniciadas en marzo de 2020 que han complicado la ejecución. Por otro, lado y dada la naturaleza tecnológica del proyecto y la necesidad de equipamiento de semiconductores, podemos identificar también complicaciones asociados a la cadena logística de este tipo de materiales necesarios para el proyecto.
Sin embargo, podemos afirmar que gracias a medidas y actuaciones definidas por los integrantes del proyecto GRI y Ágata en cuanto a mejoras en la comunicación, incremento de seguimiento del proyecto y estrecho contacto de ambos equipos han logrado paliar en gran medida estos retos provocados por el COVID 19.
En cuanto al grado de ejecución del proyecto podemos afirmar que es similar al planteado en el proyecto con diferencias existentes en cuanto a las actividades iniciadas que ha requerido algunos casos permutación con objeto de cubrir adecuadamente las interrelaciones entre ellas, propias de un proyecto de Investigación y desarrollo como es WINDIN4.0
ANUALIDAD 2022
Durante el segundo hito del proyecto WINDIN4.0 del programa “Fábrica do futuro, fábrica intelixente e sostible da industria 4.0 (cuarta convocatoria)”de GAIN, se han realizado trabajos de desarrollo que se alinean y responden a los objetivos del planteados en el proyecto en cuanto a tres ejes principales:
- Desarrollo de soluciones y subsistemas orientados al paradigma de fábrica inteligente que conformen una nueva ruta de fabricación integral de producto discreto, de gran volumen, peso y grandes dimensiones en escenarios industriales VUCA como el sector eólico. En el primer paquete de trabajo del proyecto se han estudiado el proceso integral de gestión de proyecto de fabricación de torres eólicas desde diferentes puntos de vista como la fabricación, gestión del proyecto, digitalización de proceso manuales que confluyen en la generación de conocimiento en cuanto a las posibilidades tecnológicas existentes y su aplicabilidad el sector industrial especifico que se plantea.
- Desarrollo de un entorno industrial digitalizado modular, flexible y adaptable que garantice la calidad, la seguridad y la trazabilidad en toda la cadena de valor de fabricación y que permita la evolución continua de los procesos de fabricación. En este sentido en los paquetes de trabajo 2,3 y 4 se han definido por completo y comenzado el desarrollo de algunas soluciones digitales orientadas a la gestión características estructurales del producto, gestión de procesos fabricación, digitalización de defectologia y mediambiente y gestión integral de proyectos sobre plataforma de Ágata.
- Agilizar la toma de decisiones basadas en datos y flexibilizar el entorno de fabricación, en todas sus etapas, a través de la consolidación de toda la información recogida en el centro industrial. Los trabajos realizados durante el primer hito en cuanto a la definición y desarrollos de diferentes soluciones dotarán de las herramientas necesarias para su posterior análisis y a facilitar la toma de decisiones, sin embargo, es necesario desarrollar a integrar completamente las diferentes arquitecturas para desarrollar los cuadros de mando generales que se producirá en siguientes hitos.
Entre las soluciones desarrolladas se encuentra en el centro la plataforma desarrollada por Agata Technology, denominada Plataforma Ágata. Con esta plataforma se está desarrollando flujos para:
- Mejora de la distribución de información entre departamentos de planta
- Recopilación de datos de herramientas desarrolladas dentro de la ayuda para el control productivo (como parte de un sistema SCADA), en concreto herramienta de control de la soldadura, de medición de materia prima (medición de perímetro de virolas) y control de la calidad del tratamiento superficial (granallado, metalizado y pintura) y de defectos de materia prima recibida (control de defectos de chapa)
- Desarrollo de herramienta analítica de video para el control del llenado de contenedores de residuos no peligrosos y el uso de las líneas de producción en los arcos de soldadura circular y
- Monitorización de la eficiencia energética de ciertos procesos productivos clave como la soldadura y el tratamiento superficial
Otras herramientas en desarrollo son un sistema de control de producción (MES), una plataforma para la recogida y tratamiento de información de calidad, prevención, medio ambiente y auditorías y una plataforma de control de ofertas y pedidos, con control documental y de producto del proyecto.
Además, dentro de este proyecto también se están desarrollando pruebas de concepto para el aumento de producción y automatización de procesos, así como la reducción de exposición de personal a riesgos. Los procesos seleccionados son el curado de pintura fuera de las cabinas de pintura mediante el desarrollo de un equipo de curado, el tratamiento superficial automático de pintura mediante un robot instalado en una de las cabinas de pintura y la realización del set up de soldadura en remoto.
En cuanto al grado de ejecución del proyecto podemos afirmar que es similar al planteado en el proyecto con diferencias existentes en cuanto a las actividades iniciadas que ha requerido algunos casos permutación con objeto de cubrir adecuadamente las interrelaciones entre ellas, propias de un proyecto de Investigación y Desarrollo (I+D) como es WINDIN4.0.
ANUALIDAD 2023
A continuación, podemos ver resumido el grado de avance y resultados de las atareas llevadas a cabo durante la anualidad 2023.
1.INVESTIGACIÓN DE TECNOLOGÍAS Y DEFINICIÓN DE REQUISITOS DE LA SMART FACTORY
Esta tarea se desarrolló íntegramente en la anualidad 2021 del proyecto. Durante la realización de esta, no han existido desviaciones significativas a lo propuesto en su día, continuando su revisión en la anualidad 2022 y 23 debido a su característica de evolución continua.
2.DESARROLLO DE SOLUCIONES DISRUPTIVAS PARA EL CONTROL DE PRODUCICÓN (DIGITAL MANUFACTURING)
En lo referente al Paquete de Trabajo 2, en la anualidad 2023 se han llevado modificaciones de red para adaptarse a las necesidades cambiantes de la organización. Se ha desarrollado la captación de datos de procesos sensorizados como el tratamiento superficial y la plataforma de control de la soldadura. También se realizan implantaciones de la plataforma de control de la producción (SAP MII).
3.DESARROLLO DE MODELOS AVANZADOS DE PRODUCTO DIGITAL (DIGITAL PRODUCT)
A lo largo de la tercera anualidad del proyecto WINDIN4.0, se han llevado a cabo en este paquete de trabajo tareas tales como:
- Desarrollo del módulo de PO que permite la introducción en automático de parámetros de fabricación. Mejora del módulo de gestión documental que elabora un control de revisiones de la documentación para todo el ciclo de vida del proyecto/producto.
- Revisión e implantación de algunas KPIs para su mejor definición.
- Dentro del modelo basado en cloud computing se realizaron las pruebas operativas de los módulos de Defectología, Health & Safety y Medio Ambiente.
- Programación para la lectura de los valores de los equipos de sensorización (tratamiento superficial y soladura) y muestreo en la plataforma AGATA de los consumos energéticos.
4.DISEÑO Y DESARROLLO DE PLATAFORMA INTELIGENTE DE CONTROL INDUSTRIAL
En el Paquete de Trabajo 4 del proyecto WINDIN4.0, durante la anualidad 2023 se realizan las siguientes tareas:
- Implementación de integraciones mediante el protocolo OPC-UA.
- Desarrollo e implementación de conexión OPC-UA con equipos de planta.
- Monitorización de cabinas de granalla, metalizado y pintura.
- Medición de perímetro de virolas.
- Desarrollo de KPIs e implementación de visualización en pantallas.
- Integración con WSS para monitorización de arcos de soldadura.
- Desarrollo e integración del módulo de monitorización de Zabbix.
- Optimización de los modelos BPMN:
- Alta de proyecto.
- Departamento de ingeniería.
- Departamento de calidad.
- Desarrollo e integración del modelo BPMN de producción.
- Validación y optimización de integraciones con SAP.
- Generación automática de entregables.
- Análisis y desarrollo de mejoras UX-UI.
- Ampliación de capacidades del motor de modelos de analítica.
- Desarrollo e integración de versión final de modelos de ML: Detección automática del nivel de llenado de contenedores de deshechos y de líneas de soldadura CW (Circular) sin tramo/virola.
- Desarrollo y modelado de herramienta para simulación de procesos industriales mediante BPM.
- Desarrollo e integración de widget con el nuevos GIS 3D de Hexagon.
5.CASOS DE USO AVANZADO Y POC
En este último paquete de trabajo del proyecto WINDIN4.0, durante la anualidad 2023 se han llevado a cabo el desarrollo y puesta en marcha de los PoC de procesos manuales considerados como más interesantes en las tareas del PT1 en la anualidad 2021: detección de defectos en Área 0, medición de perímetro de virolas, curado de bridas, robot de pintura, etc).
También se realiza la simulación de los procesos productivos de fábrica, así como el desarrollo e implantación de herramientas de control de producción (sensorización de cabinas de tratamiento superficial y supervisión de parámetros de soldadura).
El proyecto se ha finalizado con la realización de todas las tareas planteadas inicialmente a través de estrecha colaboración entre GRI y Agata que han podido dar solucion a los ambiciosos retos planteados en el proyecto y pudiendo afirmar que las tecnologias digitales desarrolladas cumplen los objetivos principales planteados en el proyecto;
- Suponen la creación de soluciones y subsistemas orientados al paradigma de fábrica inteligente que conforman una nueva ruta de fabricación integral de producto discreto, de gran volumen, peso y grandes dimensiones en escenarios industriales VUCA como el sector eólico.
- Generan un entorno industrial digitalizado modular, flexible y adaptable que garantice la calidad, la seguridad y la trazabilidad en toda la cadena de valor de fabricación y que permita la evolución continua de los procesos de fabricación.
- Agilizan la toma de decisiones basadas en datos y flexibilizar el entorno de fabricación, en todas sus etapas, a través de la consolidación de toda la información recogida en el centro industrial de GRI